Fabryka przyszłości 4.0 to koncepcja, która odnosi się do nowoczesnych procesów produkcyjnych, które wykorzystują zaawansowane technologie cyfrowe oraz automatyzację w celu zwiększenia efektywności i elastyczności produkcji. W centrum tej koncepcji znajduje się Internet Rzeczy, który umożliwia komunikację pomiędzy maszynami, systemami oraz ludźmi. Dzięki temu możliwe jest zbieranie danych w czasie rzeczywistym, co pozwala na szybką analizę i podejmowanie decyzji opartych na aktualnych informacjach. W fabrykach 4.0 kluczowe znaczenie mają również sztuczna inteligencja oraz uczenie maszynowe, które pozwalają na optymalizację procesów produkcyjnych i przewidywanie awarii maszyn. Wprowadzenie tych technologii wymaga jednak odpowiedniego przygotowania kadry pracowniczej oraz inwestycji w infrastrukturę technologiczną, co może stanowić wyzwanie dla wielu przedsiębiorstw.
Jakie technologie są wykorzystywane w fabrykach 4.0
W fabrykach przyszłości 4.0 wykorzystywane są różnorodne technologie, które wspierają automatyzację i cyfryzację procesów produkcyjnych. Jedną z najważniejszych jest Internet Rzeczy, który umożliwia podłączenie maszyn i urządzeń do sieci, co pozwala na ich zdalne monitorowanie i zarządzanie. Kolejną istotną technologią jest sztuczna inteligencja, która dzięki analizie dużych zbiorów danych może przewidywać awarie oraz optymalizować procesy produkcyjne. Robotyka również odgrywa kluczową rolę w fabrykach 4.0, gdzie roboty współpracujące z ludźmi wykonują powtarzalne zadania, zwiększając wydajność i bezpieczeństwo pracy. Dodatkowo technologie takie jak druk 3D czy wirtualna rzeczywistość znajdują zastosowanie w prototypowaniu oraz szkoleniu pracowników.
Jakie korzyści przynosi wdrożenie fabryk 4.0
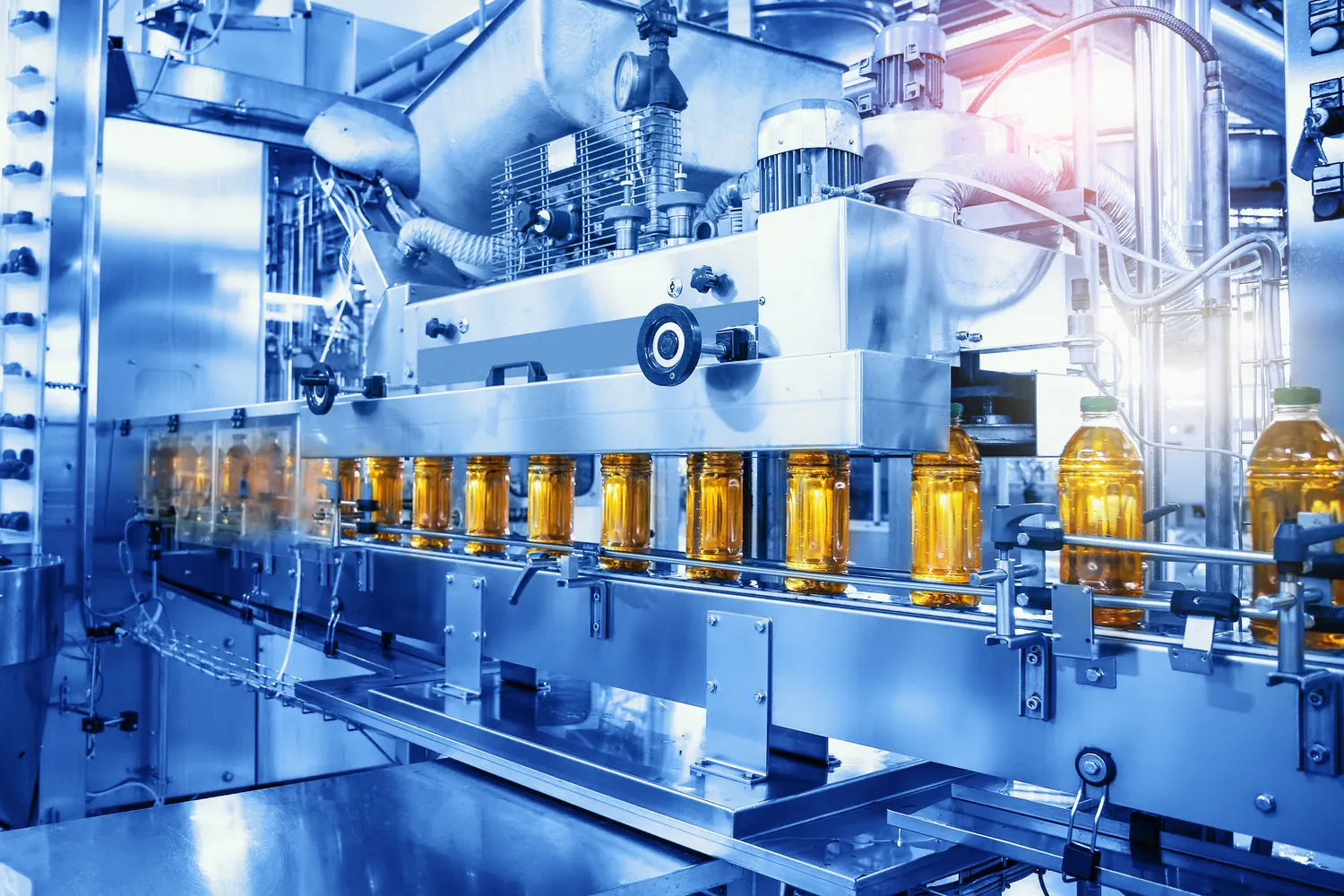
Wdrożenie koncepcji fabryk przyszłości 4.0 przynosi szereg korzyści zarówno dla przedsiębiorstw, jak i dla ich pracowników oraz klientów. Przede wszystkim zwiększa efektywność produkcji poprzez automatyzację procesów oraz optymalizację wykorzystania zasobów. Dzięki zbieraniu danych w czasie rzeczywistym możliwe jest szybkie reagowanie na zmiany w procesach produkcyjnych oraz eliminowanie potencjalnych problemów zanim te staną się poważnymi awariami. Fabryki 4.0 pozwalają także na większą elastyczność produkcji, co umożliwia szybsze dostosowywanie się do zmieniających się potrzeb rynku oraz personalizację produktów zgodnie z oczekiwaniami klientów. Dodatkowo wdrożenie nowoczesnych technologii przyczynia się do poprawy warunków pracy, ponieważ wiele niebezpiecznych lub monotonnych zadań może być wykonywanych przez maszyny lub roboty.
Jakie wyzwania stoją przed firmami przy wdrażaniu fabryk 4.0
Pomimo licznych korzyści związanych z wdrożeniem koncepcji fabryk przyszłości 4.0, przedsiębiorstwa napotykają także szereg wyzwań, które mogą utrudniać ten proces. Przede wszystkim konieczne jest znaczne inwestowanie w nowoczesne technologie oraz infrastrukturę IT, co może być dużym obciążeniem finansowym dla wielu firm, zwłaszcza małych i średnich przedsiębiorstw. Ponadto brak odpowiednio wykwalifikowanej kadry pracowniczej stanowi istotny problem, ponieważ nowe technologie wymagają umiejętności obsługi zaawansowanych systemów informatycznych oraz analizy danych. Firmy muszą także zmierzyć się z kwestiami związanymi z bezpieczeństwem danych i ochroną prywatności, ponieważ gromadzenie dużej ilości informacji wiąże się z ryzykiem ich niewłaściwego wykorzystania lub utraty.
Jakie są przykłady zastosowania fabryk 4.0 w różnych branżach
Fabryki przyszłości 4.0 znajdują zastosowanie w wielu branżach, co pokazuje ich wszechstronność oraz potencjał do transformacji tradycyjnych procesów produkcyjnych. W przemyśle motoryzacyjnym, na przykład, wykorzystanie robotów współpracujących oraz systemów monitorowania w czasie rzeczywistym pozwala na zwiększenie efektywności linii produkcyjnych oraz redukcję błędów. Dzięki temu producenci mogą szybciej wprowadzać nowe modele samochodów na rynek, dostosowując się do zmieniających się preferencji klientów. W branży elektronicznej fabryki 4.0 umożliwiają masową personalizację produktów, co jest możliwe dzięki elastycznym liniom produkcyjnym i zaawansowanym systemom zarządzania danymi. Przemysł spożywczy również korzysta z koncepcji fabryk przyszłości, gdzie technologie takie jak automatyzacja procesów pakowania oraz śledzenie jakości produktów w czasie rzeczywistym przyczyniają się do zwiększenia bezpieczeństwa żywności oraz optymalizacji procesów logistycznych.
Jakie umiejętności są potrzebne w erze fabryk 4.0
W erze fabryk przyszłości 4.0 pojawia się potrzeba posiadania nowych umiejętności przez pracowników, aby mogli skutecznie funkcjonować w zautomatyzowanym i cyfrowym środowisku produkcyjnym. Przede wszystkim kluczowe stają się umiejętności związane z obsługą nowoczesnych technologii, takich jak programowanie robotów czy analiza danych. Pracownicy muszą być w stanie interpretować dane generowane przez maszyny i systemy informatyczne, aby podejmować świadome decyzje dotyczące optymalizacji procesów produkcyjnych. Ponadto istotne są umiejętności miękkie, takie jak zdolność do pracy zespołowej oraz komunikacji, ponieważ współpraca między ludźmi a maszynami staje się coraz bardziej powszechna. Warto również zwrócić uwagę na znaczenie ciągłego kształcenia i rozwoju zawodowego, ponieważ technologia szybko się rozwija, a pracownicy muszą być gotowi na adaptację do nowych narzędzi i metod pracy.
Jakie są trendy w rozwoju fabryk 4.0 na przyszłość
Rozwój fabryk przyszłości 4.0 wiąże się z wieloma trendami, które mają potencjał do dalszej transformacji przemysłu. Jednym z najważniejszych jest rosnąca automatyzacja procesów produkcyjnych, która będzie obejmować coraz większą liczbę zadań wykonywanych przez roboty i systemy sztucznej inteligencji. To z kolei prowadzi do wzrostu wydajności oraz redukcji kosztów operacyjnych dla przedsiębiorstw. Kolejnym istotnym trendem jest rozwój technologii Internetu Rzeczy, który umożliwia jeszcze bardziej zaawansowane monitorowanie i zarządzanie procesami produkcyjnymi poprzez zbieranie danych z różnych źródeł. Warto również zauważyć rosnącą rolę analizy danych i uczenia maszynowego w podejmowaniu decyzji biznesowych, co pozwala na lepsze prognozowanie popytu oraz optymalizację łańcucha dostaw.
Jakie są kluczowe elementy strategii wdrażania fabryk 4.0
Wdrażanie koncepcji fabryk przyszłości 4.0 wymaga przemyślanej strategii, która uwzględnia różnorodne aspekty organizacyjne oraz technologiczne. Kluczowym elementem jest przeprowadzenie analizy obecnego stanu przedsiębiorstwa oraz identyfikacja obszarów wymagających poprawy lub modernizacji. Następnie należy określić cele wdrożenia technologii 4.0 oraz stworzyć plan działania uwzględniający konkretne kroki do osiągnięcia tych celów. Ważne jest także zaangażowanie wszystkich pracowników w proces zmian poprzez odpowiednie szkolenia oraz komunikację wewnętrzną, co pozwoli na budowanie kultury innowacji i otwartości na nowe rozwiązania. Kolejnym istotnym elementem strategii jest wybór odpowiednich partnerów technologicznych oraz dostawców sprzętu i oprogramowania, którzy będą wspierać firmę w procesie transformacji cyfrowej.
Jakie są perspektywy rozwoju fabryk przyszłości 4.0
Perspektywy rozwoju fabryk przyszłości 4.0 są niezwykle obiecujące i wskazują na dalszy wzrost znaczenia technologii cyfrowych w przemyśle. Z roku na rok rośnie liczba firm decydujących się na wdrożenie nowoczesnych rozwiązań technologicznych, co przyczynia się do zwiększenia konkurencyjności na rynku globalnym. W miarę jak technologie takie jak sztuczna inteligencja czy Internet Rzeczy stają się coraz bardziej dostępne i przystępne cenowo, można spodziewać się ich szerszego zastosowania w różnych branżach przemysłowych. Dodatkowo rosnące zainteresowanie kwestiami związanymi ze zrównoważonym rozwojem sprawia, że firmy będą poszukiwać innowacyjnych rozwiązań mających na celu minimalizację wpływu swojej działalności na środowisko naturalne.
Jakie są przykłady firm liderujących w zakresie fabryk 4.0
Na całym świecie można znaleźć wiele firm, które stały się liderami w zakresie wdrażania koncepcji fabryk przyszłości 4.0 i stanowią inspirację dla innych przedsiębiorstw pragnących podążać tą drogą. Przykładem może być niemiecka firma Siemens, która wykorzystuje zaawansowane technologie cyfrowe w swoich zakładach produkcyjnych, co pozwala jej na zwiększenie efektywności operacyjnej oraz elastyczności produkcji. Inny przykład to amerykański producent samochodów Ford, który inwestuje w automatyzację swoich linii produkcyjnych oraz rozwija technologie związane z Internetem Rzeczy w celu optymalizacji procesów produkcyjnych i poprawy jakości produktów. W branży elektroniki warto wspomnieć o firmie Bosch, która stosuje rozwiązania oparte na sztucznej inteligencji i analizie danych do monitorowania wydajności swoich zakładów produkcyjnych oraz przewidywania awarii maszyn przed ich wystąpieniem.