Budowa maszyn pneumatycznych opiera się na kilku kluczowych elementach, które współpracują ze sobą, aby zapewnić efektywne działanie systemów wykorzystujących sprężone powietrze. Podstawowym komponentem jest sprężarka, która odpowiada za wytwarzanie sprężonego powietrza. Sprężarki mogą mieć różne typy, takie jak tłokowe, śrubowe czy membranowe, a ich wybór zależy od specyficznych potrzeb aplikacji. Kolejnym istotnym elementem są zbiorniki ciśnieniowe, które magazynują sprężone powietrze i pozwalają na jego równomierne dostarczanie do układów pneumatycznych. W systemach pneumatycznych niezbędne są również zawory, które kontrolują przepływ powietrza oraz kierunek jego przepływu. Zawory te mogą być ręczne lub automatyczne, a ich odpowiedni dobór ma kluczowe znaczenie dla wydajności całego systemu. Rury i przewody pneumatyczne stanowią kolejny ważny element budowy maszyn pneumatycznych, umożliwiając transport sprężonego powietrza do różnych części układu.
Jakie są zalety i wady maszyn pneumatycznych
Maszyny pneumatyczne mają wiele zalet, które przyczyniają się do ich popularności w różnych branżach przemysłowych. Jedną z głównych korzyści jest ich prostota konstrukcji oraz łatwość obsługi. Dzięki temu można je szybko wdrożyć w procesach produkcyjnych. Dodatkowo maszyny te charakteryzują się dużą niezawodnością i niskimi kosztami utrzymania, co czyni je atrakcyjnym rozwiązaniem dla wielu przedsiębiorstw. Ponadto systemy pneumatyczne są stosunkowo bezpieczne w użytkowaniu, ponieważ nie wymagają stosowania substancji łatwopalnych ani toksycznych. Niemniej jednak istnieją również pewne wady związane z użyciem maszyn pneumatycznych. Jednym z głównych ograniczeń jest to, że efektywność energetyczna tych systemów może być niższa w porównaniu do innych technologii, takich jak hydraulika czy elektryka. W przypadku długotrwałego użytkowania może to prowadzić do wyższych kosztów eksploatacyjnych. Dodatkowo sprężone powietrze ma ograniczoną moc, co może być niewystarczające w bardziej wymagających aplikacjach.
Jakie są zastosowania maszyn pneumatycznych w przemyśle
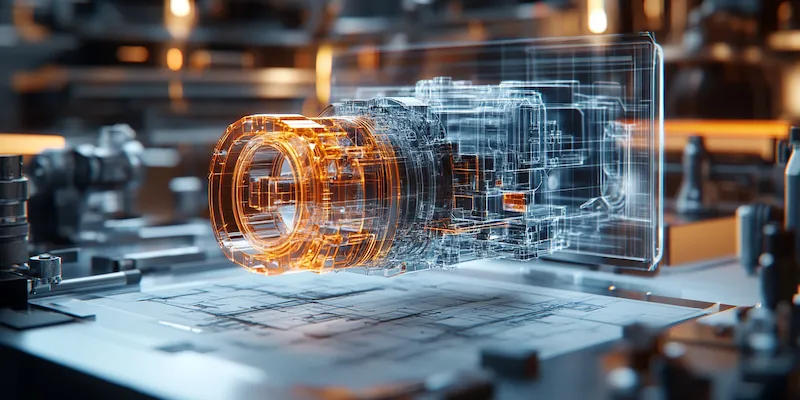
Maszyny pneumatyczne znajdują szerokie zastosowanie w różnych dziedzinach przemysłu dzięki swojej wszechstronności i efektywności. W przemyśle produkcyjnym są wykorzystywane do automatyzacji procesów montażowych oraz pakowania produktów. Siłowniki pneumatyczne napędzają różnego rodzaju urządzenia, takie jak prasy czy roboty przemysłowe, co pozwala na zwiększenie wydajności produkcji oraz redukcję kosztów pracy. W branży motoryzacyjnej maszyny pneumatyczne służą do malowania i lakierowania pojazdów, a także do wykonywania precyzyjnych operacji montażowych. W logistyce i magazynowaniu wykorzystuje się je do podnoszenia i transportowania ciężkich ładunków za pomocą systemów podnośników pneumatycznych. Kolejnym obszarem zastosowań jest przemysł spożywczy, gdzie maszyny te są używane do pakowania żywności oraz transportu produktów sypkich lub płynnych. Dzięki swoim właściwościom maszyny pneumatyczne są również wykorzystywane w medycynie i farmacji do precyzyjnego dawkowania leków oraz w laboratoriach chemicznych do obsługi substancji niebezpiecznych. Ich elastyczność sprawia, że znajdują zastosowanie również w branży budowlanej, gdzie służą m.in.
Jakie są nowoczesne technologie w budowie maszyn pneumatycznych
Nowoczesne technologie mają ogromny wpływ na rozwój budowy maszyn pneumatycznych, co przekłada się na ich wydajność i funkcjonalność. W ostatnich latach nastąpił znaczny postęp w zakresie automatyzacji procesów związanych z obsługą systemów pneumatycznych. Wprowadzenie inteligentnych czujników oraz systemów monitorujących pozwala na bieżące śledzenie parametrów pracy maszyn oraz optymalizację ich działania. Dzięki temu możliwe jest szybkie reagowanie na ewentualne awarie czy zmiany warunków pracy, co zwiększa bezpieczeństwo i niezawodność całych układów. Dodatkowo rozwój technologii materiałowych przyczynił się do produkcji lżejszych i bardziej wytrzymałych komponentów maszyn pneumatycznych, co wpływa na ich dłuższą żywotność oraz mniejsze zużycie energii. Coraz częściej stosowane są także rozwiązania oparte na sztucznej inteligencji i uczeniu maszynowym, które umożliwiają przewidywanie awarii oraz automatyczne dostosowywanie parametrów pracy systemu do zmieniających się warunków otoczenia.
Jakie są kluczowe zasady bezpieczeństwa w maszynach pneumatycznych
Bezpieczeństwo w pracy z maszynami pneumatycznymi jest niezwykle istotne, ponieważ niewłaściwe użytkowanie tych urządzeń może prowadzić do poważnych wypadków. Kluczową zasadą jest zapewnienie, że wszystkie komponenty systemu są odpowiednio dobrane i spełniają normy bezpieczeństwa. Pracownicy powinni być przeszkoleni w zakresie obsługi maszyn pneumatycznych oraz zasad ich działania, co pozwoli na uniknięcie niebezpiecznych sytuacji. Ważne jest również regularne przeprowadzanie przeglądów technicznych oraz konserwacji urządzeń, aby upewnić się, że działają one prawidłowo i nie mają uszkodzeń, które mogłyby prowadzić do awarii. W przypadku pracy z wysokim ciśnieniem sprężonego powietrza należy stosować odpowiednie środki ochrony osobistej, takie jak gogle ochronne czy rękawice, aby zminimalizować ryzyko urazów. Kolejnym aspektem bezpieczeństwa jest właściwe oznakowanie strefy pracy oraz umieszczenie informacji dotyczących potencjalnych zagrożeń. Warto również wdrożyć procedury awaryjne, które będą określały kroki do podjęcia w przypadku wystąpienia niebezpiecznej sytuacji.
Jakie są różnice między maszynami pneumatycznymi a hydraulicznymi
Maszyny pneumatyczne i hydrauliczne to dwa różne typy systemów wykorzystywanych w przemyśle, które mają swoje unikalne cechy i zastosowania. Główna różnica między nimi polega na medium roboczym; maszyny pneumatyczne wykorzystują sprężone powietrze, podczas gdy maszyny hydrauliczne działają na zasadzie cieczy pod ciśnieniem. Dzięki temu maszyny hydrauliczne mogą generować znacznie większe siły niż ich pneumatyczne odpowiedniki, co czyni je bardziej odpowiednimi do ciężkich zastosowań, takich jak prasy czy dźwigi. Z drugiej strony maszyny pneumatyczne są zazwyczaj lżejsze i prostsze w budowie, co sprawia, że są bardziej mobilne i łatwiejsze w obsłudze. Kolejną różnicą jest efektywność energetyczna; systemy hydrauliczne mogą być bardziej wydajne w długoterminowym użytkowaniu, podczas gdy maszyny pneumatyczne często wymagają więcej energii ze względu na straty związane z kompresją powietrza. W kontekście bezpieczeństwa maszyny pneumatyczne są mniej ryzykowne w przypadku wycieków, ponieważ sprężone powietrze nie jest substancją łatwopalną ani toksyczną.
Jakie są najczęstsze problemy z maszynami pneumatycznymi
Podczas użytkowania maszyn pneumatycznych mogą występować różnorodne problemy, które wpływają na ich wydajność oraz niezawodność. Jednym z najczęstszych problemów jest wyciek sprężonego powietrza, który może prowadzić do obniżenia ciśnienia w systemie oraz zwiększenia kosztów eksploatacyjnych. Wyciek może wystąpić na skutek uszkodzenia przewodów lub nieszczelności w zaworach i połączeniach. Innym powszechnym problemem jest zanieczyszczenie sprężonego powietrza, które może prowadzić do uszkodzenia komponentów układu oraz obniżenia efektywności działania maszyn. Aby temu zapobiec, warto stosować filtry powietrza oraz regularnie przeprowadzać konserwację urządzeń. Problemy z siłownikami pneumatycznymi mogą również występować z powodu niewłaściwego ustawienia lub zużycia uszczelek, co może prowadzić do utraty mocy roboczej. Dodatkowo niewłaściwe ciśnienie robocze może powodować niestabilność działania systemu oraz jego awarie.
Jakie są przyszłościowe kierunki rozwoju technologii pneumatycznych
Przyszłość technologii pneumatycznych zapowiada się obiecująco dzięki ciągłemu rozwojowi innowacyjnych rozwiązań oraz rosnącemu zainteresowaniu automatyzacją procesów przemysłowych. Jednym z kluczowych kierunków rozwoju jest integracja systemów pneumatycznych z technologią Internetu Rzeczy (IoT), co pozwoli na zdalne monitorowanie i zarządzanie urządzeniami w czasie rzeczywistym. Dzięki temu możliwe będzie szybsze wykrywanie problemów oraz optymalizacja procesów produkcyjnych. Ponadto rozwój sztucznej inteligencji umożliwi lepszą analizę danych zbieranych przez czujniki, co przyczyni się do poprawy efektywności działania systemów pneumatycznych oraz przewidywania awarii przed ich wystąpieniem. Innowacyjne materiały i technologie produkcji komponentów maszyn pneumatycznych również będą miały znaczący wpływ na ich przyszłość; lżejsze i bardziej wytrzymałe materiały pozwolą na tworzenie bardziej kompaktowych i efektywnych układów. W kontekście zrównoważonego rozwoju coraz większą rolę będą odgrywać rozwiązania ekologiczne, takie jak wykorzystanie odnawialnych źródeł energii do generowania sprężonego powietrza czy recykling materiałów używanych w produkcji maszyn pneumatycznych.
Jakie są najpopularniejsze marki produkujące maszyny pneumatyczne
Na rynku istnieje wiele renomowanych marek zajmujących się produkcją maszyn pneumatycznych, które zdobyły uznanie dzięki jakości swoich produktów oraz innowacyjnym rozwiązaniom technologicznym. Jedną z najbardziej znanych firm jest Festo, która oferuje szeroką gamę komponentów pneumatycznych oraz systemów automatyzacji przemysłowej. Festo wyróżnia się wysoką jakością wykonania oraz zaawansowanymi technologiami, co czyni ją liderem w branży. Innym znaczącym producentem jest SMC Corporation, który specjalizuje się w projektowaniu i produkcji elementów układów pneumatycznych takich jak siłowniki, zawory czy filtry powietrza. SMC cieszy się dużym uznaniem ze względu na innowacyjne podejście do rozwoju produktów oraz ich niezawodność. Warto również wspomnieć o firmie Parker Hannifin, która oferuje kompleksowe rozwiązania w zakresie technologii ruchu i kontroli płynów; jej oferta obejmuje zarówno maszyny pneumatyczne, jak i hydrauliczne. Inne popularne marki to Bosch Rexroth czy Norgren, które również dostarczają wysokiej jakości komponenty dla przemysłu pneumatycznego.