Budowa maszyn to złożony proces, który obejmuje wiele różnych elementów i komponentów. W każdej maszynie można wyróżnić kilka podstawowych części, które są kluczowe dla jej funkcjonowania. Przede wszystkim należy zwrócić uwagę na układ napędowy, który odpowiada za przekazywanie energii z silnika do pozostałych elementów maszyny. W skład układu napędowego wchodzą takie elementy jak silniki, przekładnie oraz wały. Kolejnym istotnym elementem jest układ sterujący, który pozwala na kontrolowanie pracy maszyny. W jego skład wchodzą różnego rodzaju czujniki, przekaźniki oraz systemy komputerowe. Oprócz tego ważne są także elementy konstrukcyjne, takie jak ramy, obudowy czy łożyska, które zapewniają stabilność i trwałość całej maszyny. Nie można zapominać o systemach zabezpieczeń, które chronią zarówno maszynę, jak i operatora przed ewentualnymi awariami czy wypadkami.
Jakie są rodzaje maszyn w budownictwie
Budowa maszyn w branży budowlanej obejmuje wiele różnych typów urządzeń, które mają na celu ułatwienie prac budowlanych oraz zwiększenie ich efektywności. Do najpopularniejszych rodzajów maszyn budowlanych zalicza się koparki, które służą do wykopów oraz przemieszczania ziemi. Innym istotnym rodzajem są ładowarki, które umożliwiają załadunek materiałów sypkich na ciężarówki lub inne pojazdy transportowe. Dźwigi to kolejna kategoria maszyn budowlanych, które są niezbędne do podnoszenia ciężkich elementów konstrukcyjnych na wysokość. Warto również wspomnieć o betoniarkach, które są używane do mieszania betonu na placu budowy. Maszyny te charakteryzują się różnymi parametrami technicznymi oraz zastosowaniem w zależności od specyfiki danego projektu budowlanego. W ostatnich latach coraz większą popularnością cieszą się także maszyny zautomatyzowane oraz roboty budowlane, które mogą wykonywać skomplikowane zadania bez potrzeby ludzkiej interwencji.
Jakie są etapy projektowania maszyn przemysłowych
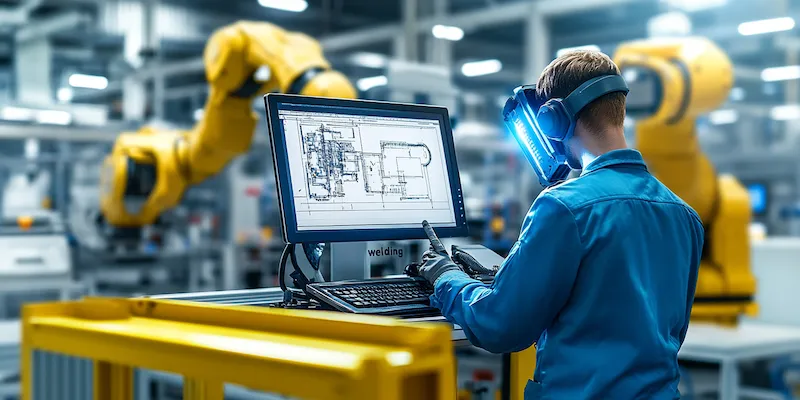
Projektowanie maszyn przemysłowych to skomplikowany proces, który wymaga uwzględnienia wielu czynników technicznych oraz ekonomicznych. Pierwszym etapem jest analiza potrzeb klienta oraz określenie wymagań dotyczących maszyny. Na tym etapie inżynierowie zbierają informacje o zastosowaniu maszyny, jej wydajności oraz warunkach pracy. Następnie przechodzi się do fazy koncepcyjnej, gdzie tworzone są wstępne projekty oraz modele 3D maszyny. W tej fazie ważne jest również przeprowadzenie analizy kosztów produkcji oraz oceny opłacalności projektu. Kolejnym krokiem jest szczegółowe projektowanie poszczególnych komponentów maszyny oraz przygotowanie dokumentacji technicznej. Po zakończeniu etapu projektowania następuje produkcja prototypu, który jest testowany pod kątem wydajności i bezpieczeństwa. Ostatnim etapem jest wdrożenie maszyny do produkcji seryjnej oraz jej dostarczenie do klienta.
Jakie są nowoczesne technologie w budowie maszyn
Nowoczesne technologie odgrywają kluczową rolę w budowie maszyn i znacząco wpływają na ich wydajność oraz funkcjonalność. Jednym z najważniejszych trendów jest automatyzacja procesów produkcyjnych, która pozwala na zmniejszenie kosztów pracy oraz zwiększenie precyzji wykonania poszczególnych komponentów. Wykorzystanie robotów przemysłowych staje się coraz bardziej powszechne w fabrykach zajmujących się produkcją maszyn. Dzięki nim możliwe jest wykonywanie powtarzalnych zadań z dużą dokładnością i szybkością. Kolejną innowacją są technologie druku 3D, które umożliwiają szybkie prototypowanie oraz produkcję skomplikowanych części maszyn bez potrzeby stosowania tradycyjnych metod obróbczych. Warto również zwrócić uwagę na rozwój systemów monitorowania i diagnostyki maszyn, które pozwalają na bieżąco śledzić ich stan techniczny oraz przewidywać potencjalne awarie. Technologie te przyczyniają się do zwiększenia efektywności produkcji oraz poprawy jakości wyrobów końcowych.
Jakie są kluczowe zasady bezpieczeństwa w budowie maszyn
Bezpieczeństwo w budowie maszyn jest niezwykle istotnym zagadnieniem, które ma na celu ochronę zarówno pracowników, jak i samego sprzętu. W pierwszej kolejności należy zwrócić uwagę na odpowiednie szkolenie personelu, które powinno obejmować zarówno teoretyczne, jak i praktyczne aspekty obsługi maszyn. Każdy operator powinien być świadomy potencjalnych zagrożeń związanych z pracą na danym urządzeniu oraz znać procedury awaryjne. Kolejnym kluczowym elementem jest stosowanie odpowiednich środków ochrony osobistej, takich jak kaski, rękawice czy okulary ochronne, które mogą znacznie zmniejszyć ryzyko urazów. Ważne jest również regularne przeprowadzanie przeglądów technicznych maszyn oraz ich konserwacja, co pozwala na wykrycie ewentualnych usterek przed ich wystąpieniem. Dodatkowo, należy przestrzegać zasad ergonomii w miejscu pracy, aby zminimalizować ryzyko kontuzji związanych z długotrwałym użytkowaniem maszyn. Warto także wdrażać systemy monitorowania bezpieczeństwa, które umożliwiają bieżące śledzenie warunków pracy oraz identyfikację potencjalnych zagrożeń.
Jakie są najczęstsze awarie maszyn i ich przyczyny
Awarie maszyn to nieodłączny element ich eksploatacji, a ich występowanie może prowadzić do poważnych problemów w procesie produkcyjnym. Najczęściej spotykanymi awariami są uszkodzenia układów hydraulicznych oraz elektrycznych. W przypadku układów hydraulicznych przyczyną awarii mogą być nieszczelności w przewodach, zużycie uszczelek lub zanieczyszczenia oleju hydraulicznego. Z kolei w układach elektrycznych najczęściej dochodzi do przepaleń przewodów, uszkodzeń silników czy awarii czujników. Innym częstym problemem są usterki mechaniczne, takie jak pęknięcia elementów konstrukcyjnych czy zużycie łożysk. Przyczyną tych awarii często jest niewłaściwa eksploatacja maszyny, brak regularnej konserwacji oraz niewłaściwe ustawienia parametrów pracy. Warto również zwrócić uwagę na wpływ warunków atmosferycznych na działanie maszyn, szczególnie w przypadku urządzeń pracujących na zewnątrz. Ekstremalne temperatury czy wilgotność mogą negatywnie wpływać na materiały użyte w konstrukcji maszyny.
Jakie są zalety i wady różnych typów napędów w maszynach
Wybór odpowiedniego napędu dla maszyny ma kluczowe znaczenie dla jej wydajności oraz funkcjonalności. Istnieje wiele różnych typów napędów, a każdy z nich ma swoje zalety i wady. Napędy elektryczne są jednymi z najczęściej stosowanych rozwiązań ze względu na swoją efektywność energetyczną oraz prostotę obsługi. Charakteryzują się one cichą pracą oraz niskimi kosztami eksploatacji, jednak wymagają dostępu do źródła energii elektrycznej. Z kolei napędy spalinowe są bardziej mobilne i niezależne od infrastruktury energetycznej, co czyni je idealnym rozwiązaniem do zastosowań terenowych. Ich wadą jest jednak większa emisja spalin oraz hałas podczas pracy. Napędy hydrauliczne oferują dużą moc przy kompaktowych rozmiarach, co sprawia, że są często wykorzystywane w ciężkim sprzęcie budowlanym. Ich ograniczeniem jest natomiast konieczność stosowania specjalistycznych płynów hydraulicznych oraz ryzyko wycieków.
Jakie są przyszłościowe kierunki rozwoju technologii budowy maszyn
Przyszłość budowy maszyn zapowiada się niezwykle interesująco dzięki dynamicznemu rozwojowi technologii oraz rosnącym wymaganiom rynku. Jednym z kluczowych trendów jest dalsza automatyzacja procesów produkcyjnych, która pozwala na zwiększenie efektywności oraz redukcję kosztów pracy. Wprowadzenie sztucznej inteligencji do procesów projektowania i produkcji maszyn umożliwia szybsze podejmowanie decyzji oraz optymalizację procesów produkcyjnych. Kolejnym istotnym kierunkiem rozwoju jest integracja Internetu Rzeczy (IoT) z maszynami przemysłowymi, co pozwala na bieżące monitorowanie ich stanu technicznego oraz przewidywanie ewentualnych awarii. Dzięki temu możliwe będzie wdrażanie proaktywnych działań konserwacyjnych, co przyczyni się do zwiększenia dostępności maszyn i obniżenia kosztów utrzymania. Również rozwój materiałów kompozytowych i lekkich stopów metali otwiera nowe możliwości w zakresie konstrukcji maszyn o zwiększonej wytrzymałości przy jednoczesnym zmniejszeniu ich masy. Warto również zwrócić uwagę na rosnącą popularność rozwiązań ekologicznych, takich jak napędy elektryczne czy hybrydowe, które mają na celu ograniczenie negatywnego wpływu przemysłu na środowisko naturalne.
Jakie są najważniejsze trendy w projektowaniu nowoczesnych maszyn
Projektowanie nowoczesnych maszyn podlega ciągłym zmianom i ewolucji w odpowiedzi na rosnące wymagania rynku oraz postęp technologiczny. Jednym z najważniejszych trendów jest modularność konstrukcji maszyn, która pozwala na łatwe dostosowywanie urządzeń do zmieniających się potrzeb użytkowników. Dzięki modułowej budowie możliwe jest szybkie wymienianie lub dodawanie nowych komponentów bez konieczności przeprowadzania skomplikowanych modyfikacji całej maszyny. Kolejnym istotnym trendem jest zastosowanie zaawansowanych systemów sterowania opartych na sztucznej inteligencji i uczeniu maszynowym, które pozwalają na automatyzację wielu procesów produkcyjnych oraz optymalizację pracy urządzeń w czasie rzeczywistym. W projektowaniu nowoczesnych maszyn coraz większą rolę odgrywa również ergonomia, która ma na celu zapewnienie komfortu pracy operatora oraz minimalizację ryzyka urazów związanych z długotrwałym użytkowaniem sprzętu. Warto także zwrócić uwagę na rozwój technologii druku 3D, która umożliwia szybkie prototypowanie i produkcję skomplikowanych części maszyn o wysokiej precyzji wykonania.
Jakie są wyzwania związane z utrzymaniem nowoczesnych maszyn
Utrzymanie nowoczesnych maszyn wiąże się z wieloma wyzwaniami wynikającymi z ich skomplikowanej budowy oraz zaawansowanej technologii zastosowanej w ich konstrukcji. Jednym z głównych problemów jest konieczność regularnego przeprowadzania przeglądów technicznych oraz konserwacji poszczególnych komponentów maszyny, co wymaga odpowiednich umiejętności i wiedzy ze strony personelu serwisowego. W miarę jak technologie stają się coraz bardziej zaawansowane, wzrasta również potrzeba ciągłego kształcenia pracowników zajmujących się obsługą i naprawą tych urządzeń. Innym wyzwaniem jest dostępność części zamiennych do nowoczesnych maszyn, które mogą być drogie lub trudne do zdobycia w przypadku starszych modeli lub specjalistycznego sprzętu. Ponadto wiele nowoczesnych urządzeń korzysta z zaawansowanych systemów monitorowania stanu technicznego, co generuje dodatkowe dane do analizy i interpretacji przez personel serwisowy. Zarządzanie tymi informacjami może być czasochłonne i wymaga odpowiednich narzędzi analitycznych oraz wiedzy technicznej.