Destylarka do rozpuszczalnika to urządzenie, które wykorzystuje proces destylacji do oddzielania różnych składników chemicznych. Proces ten polega na podgrzewaniu cieczy, co powoduje jej parowanie, a następnie skraplaniu pary w celu uzyskania czystego rozpuszczalnika. W praktyce oznacza to, że destylarka jest w stanie oddzielić substancje o różnych temperaturach wrzenia, co jest kluczowe w wielu zastosowaniach przemysłowych oraz laboratoryjnych. W przypadku destylacji prostej, ciecz jest podgrzewana w zbiorniku, a para przechodzi przez chłodnicę, gdzie skrapla się z powrotem do postaci cieczy. W bardziej zaawansowanych systemach można stosować destylację frakcyjną, która pozwala na jeszcze skuteczniejsze oddzielanie składników o zbliżonych temperaturach wrzenia. Dzięki temu możliwe jest uzyskanie wysokiej czystości rozpuszczalników, co ma ogromne znaczenie w chemii analitycznej oraz w produkcji farb, lakierów czy kosmetyków.
Jakie są najważniejsze elementy destylarki do rozpuszczalnika
Każda destylarka do rozpuszczalnika składa się z kilku kluczowych elementów, które współpracują ze sobą, aby umożliwić efektywny proces destylacji. Podstawowym komponentem jest zbiornik, w którym umieszczana jest ciecz do destylacji. Zbiornik ten musi być wykonany z materiałów odpornych na działanie chemikaliów oraz wysokich temperatur. Kolejnym istotnym elementem jest źródło ciepła, które może być elektryczne lub gazowe, a jego zadaniem jest podgrzewanie cieczy do momentu jej wrzenia. Ważnym elementem jest również chłodnica, która schładza parę i skrapla ją z powrotem do postaci cieczy. Chłodnice mogą mieć różne kształty i rozmiary, a ich efektywność wpływa na wydajność całego procesu. Dodatkowo wiele nowoczesnych destylarek wyposażonych jest w systemy kontroli temperatury oraz ciśnienia, co pozwala na precyzyjne dostosowanie warunków pracy urządzenia. Nie można zapomnieć o zbiorniku na produkt końcowy, który gromadzi oczyszczony rozpuszczalnik i umożliwia jego dalsze wykorzystanie.
Jakie są zastosowania destylarki do rozpuszczalnika w przemyśle
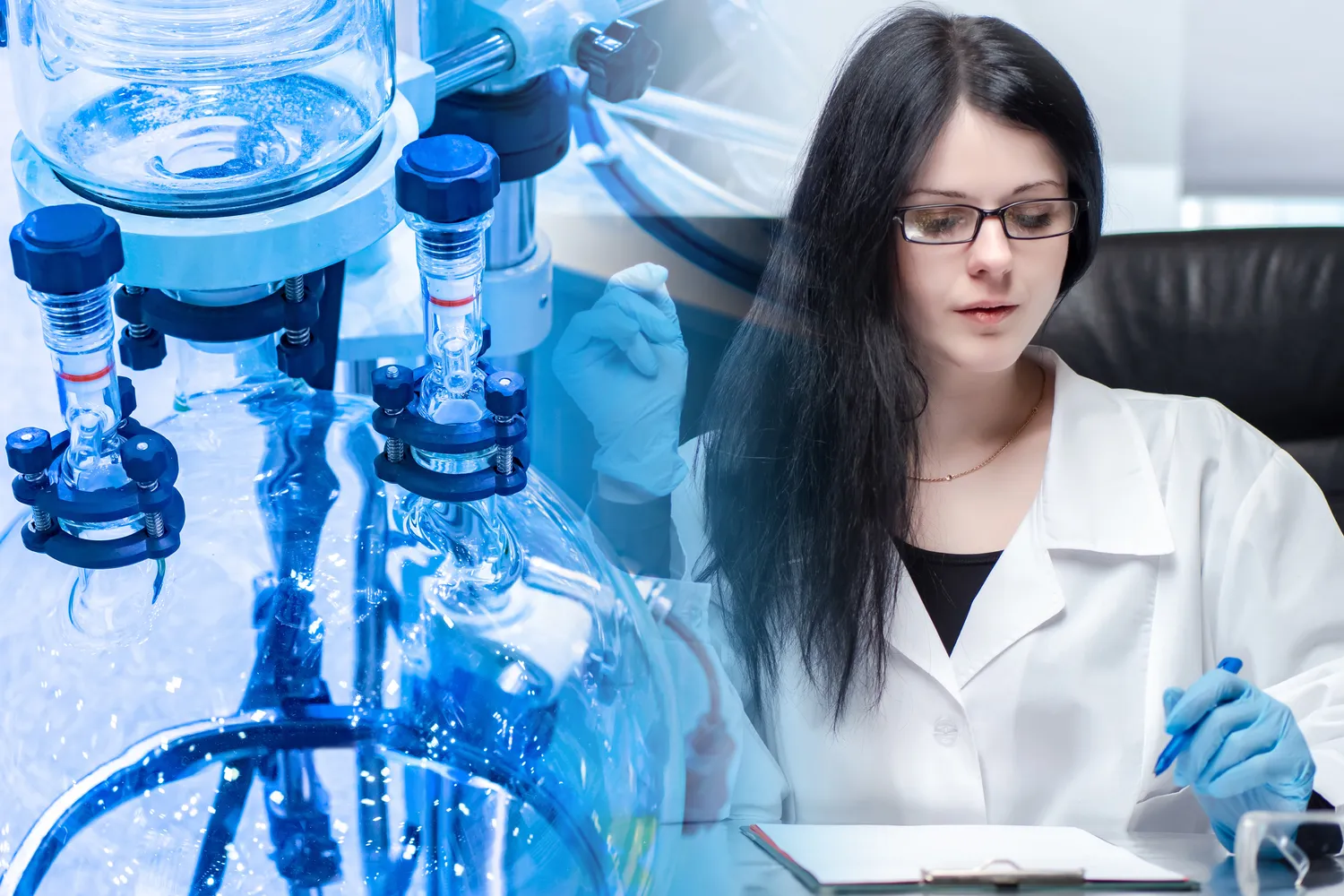
Destylarka do rozpuszczalnika znajduje szerokie zastosowanie w różnych branżach przemysłowych oraz laboratoriach badawczych. Przede wszystkim wykorzystywana jest w przemyśle chemicznym do oczyszczania surowców oraz produkcji wysokiej jakości substancji chemicznych. Dzięki możliwości separacji składników o różnych temperaturach wrzenia, destylarki pozwalają na uzyskiwanie czystych rozpuszczalników, które są niezbędne w wielu procesach produkcyjnych. W branży farmaceutycznej destylacja odgrywa kluczową rolę w produkcji leków oraz substancji czynnych, gdzie czystość składników ma fundamentalne znaczenie dla jakości finalnego produktu. Ponadto destylarki są wykorzystywane w przemyśle kosmetycznym do produkcji perfum oraz innych kosmetyków zawierających lotne substancje zapachowe. W laboratoriach analitycznych destylacja służy jako metoda oczyszczania próbek przed ich dalszą analizą chemiczną. Coraz częściej destylarki stosowane są także w procesach recyklingu rozpuszczalników, co przyczynia się do zmniejszenia odpadów i oszczędności surowców naturalnych.
Jakie są korzyści z używania destylarki do rozpuszczalnika
Korzystanie z destylarki do rozpuszczalnika przynosi wiele korzyści zarówno dla przemysłu, jak i dla środowiska naturalnego. Przede wszystkim umożliwia ona uzyskanie wysokiej jakości rozpuszczalników o dużej czystości, co jest kluczowe dla wielu procesów produkcyjnych oraz badań laboratoryjnych. Dzięki temu możliwe jest osiągnięcie lepszych wyników analitycznych oraz wyższej jakości produktów końcowych. Ponadto stosowanie destylarek pozwala na recykling zużytych rozpuszczalników, co znacząco redukuje ilość odpadów chemicznych generowanych przez przemysł. Recykling przyczynia się także do oszczędności surowców naturalnych oraz zmniejszenia kosztów produkcji poprzez ponowne wykorzystanie tych samych materiałów. Korzystanie z destylarek wpływa również pozytywnie na ochronę środowiska poprzez ograniczenie emisji szkodliwych substancji chemicznych i zmniejszenie zużycia energii potrzebnej do produkcji nowych rozpuszczalników. Dodatkowo nowoczesne urządzenia często wyposażone są w systemy monitorujące i kontrolujące procesy technologiczne, co zwiększa bezpieczeństwo pracy oraz minimalizuje ryzyko wystąpienia awarii czy niebezpiecznych sytuacji podczas użytkowania sprzętu.
Jakie są różnice między destylarką do rozpuszczalnika a innymi urządzeniami
Wybór odpowiedniego urządzenia do destylacji jest kluczowy dla efektywności procesów chemicznych, dlatego warto zrozumieć różnice między destylarką do rozpuszczalnika a innymi typami urządzeń. Destylarka do rozpuszczalnika jest specjalnie zaprojektowana do separacji cieczy na podstawie ich temperatur wrzenia, co czyni ją idealnym narzędziem w przemyśle chemicznym i farmaceutycznym. W przeciwieństwie do prostych systemów filtracji, które usuwają zanieczyszczenia mechaniczne, destylacja pozwala na oddzielanie substancji chemicznych o różnych właściwościach fizycznych. Innym popularnym urządzeniem jest ekstraktor, który wykorzystuje rozpuszczalniki do wyciągania substancji czynnych z surowców naturalnych. Ekstrakcja może być bardziej efektywna w przypadku niektórych związków, ale nie oferuje tak wysokiej czystości jak destylacja. Ponadto istnieją również kolumny destylacyjne, które umożliwiają bardziej zaawansowane procesy destylacji frakcyjnej, jednak są one zazwyczaj droższe i bardziej skomplikowane w obsłudze. Warto także zwrócić uwagę na to, że destylarki mogą mieć różne rozmiary i moce, co wpływa na ich zastosowanie w małych laboratoriach lub dużych zakładach przemysłowych.
Jakie są najczęstsze problemy związane z użytkowaniem destylarki do rozpuszczalnika
Podczas użytkowania destylarki do rozpuszczalnika mogą wystąpić różnorodne problemy, które mogą wpłynąć na efektywność procesu oraz jakość uzyskiwanego produktu. Jednym z najczęstszych problemów jest niewłaściwa kontrola temperatury, która może prowadzić do niepełnej destylacji lub przegrzewania cieczy. Zbyt wysoka temperatura może spowodować degradację składników chemicznych, co negatywnie wpłynie na czystość końcowego rozpuszczalnika. Inny problem to zatykanie się chłodnicy lub rurki odprowadzającej parę, co może prowadzić do obniżenia wydajności całego systemu. Regularne czyszczenie i konserwacja tych elementów są kluczowe dla zapewnienia ich prawidłowego działania. Dodatkowo, niewłaściwe ustawienia ciśnienia mogą prowadzić do nieefektywnego oddzielania składników oraz zwiększonego ryzyka awarii. Ważne jest również monitorowanie jakości używanych surowców, ponieważ zanieczyszczone lub nieodpowiednie materiały mogą wpływać na proces destylacji. W przypadku zauważenia jakichkolwiek anomalii w działaniu urządzenia, należy natychmiast podjąć działania naprawcze oraz skonsultować się z producentem lub specjalistą w dziedzinie technologii chemicznej.
Jakie są koszty zakupu i eksploatacji destylarki do rozpuszczalnika
Koszty zakupu i eksploatacji destylarki do rozpuszczalnika mogą się znacznie różnić w zależności od wielu czynników, takich jak typ urządzenia, jego wydajność oraz dodatkowe funkcje technologiczne. Na rynku dostępne są zarówno proste modele laboratoryjne, które można nabyć za stosunkowo niewielką kwotę, jak i zaawansowane systemy przemysłowe, których cena może sięgać nawet kilkuset tysięcy złotych. Przy wyborze odpowiedniej destylarki warto zwrócić uwagę na jej parametry techniczne oraz możliwości dostosowania do specyficznych potrzeb produkcji. Koszty eksploatacji obejmują nie tylko zużycie energii elektrycznej lub gazu potrzebnego do podgrzewania cieczy, ale także koszty konserwacji oraz ewentualnych napraw. Regularne przeglądy techniczne są kluczowe dla utrzymania sprawności urządzenia oraz minimalizacji ryzyka awarii. Dodatkowo warto uwzględnić koszty związane z zakupem materiałów eksploatacyjnych oraz chemikaliów wykorzystywanych w procesie destylacji. W dłuższej perspektywie czasowej inwestycja w wysokiej jakości destylarkę może przynieść znaczne oszczędności dzięki możliwości recyklingu rozpuszczalników oraz poprawie jakości produktów końcowych.
Jakie są najnowsze technologie w dziedzinie destylacji rozpuszczalników
W ostatnich latach rozwój technologii w dziedzinie destylacji rozpuszczalników znacząco przyspieszył, co przyczyniło się do powstania nowoczesnych systemów o wyższej wydajności i efektywności energetycznej. Jednym z najważniejszych trendów jest automatyzacja procesów destylacyjnych, która pozwala na precyzyjne monitorowanie i kontrolowanie parametrów pracy urządzenia bez konieczności stałej obsługi ze strony operatora. Dzięki zastosowaniu zaawansowanych czujników i systemów sterujących możliwe jest osiągnięcie optymalnych warunków pracy oraz minimalizacja ryzyka błędów ludzkich. Kolejnym innowacyjnym rozwiązaniem są systemy odzysku ciepła, które pozwalają na ponowne wykorzystanie energii generowanej podczas procesu destylacji. Takie podejście przyczynia się do zmniejszenia kosztów operacyjnych oraz ograniczenia emisji CO2 związanej z produkcją energii. Warto również wspomnieć o rozwijających się technologiach membranowych, które stanowią alternatywę dla tradycyjnej destylacji poprzez separację składników na poziomie molekularnym. Te nowoczesne metody mogą być szczególnie korzystne w przypadku substancji o bliskich temperaturach wrzenia lub w sytuacjach wymagających minimalizacji strat materiałowych.
Jakie są regulacje prawne dotyczące używania destylarek do rozpuszczalnika
Używanie destylarek do rozpuszczalnika wiąże się z przestrzeganiem szeregu regulacji prawnych mających na celu zapewnienie bezpieczeństwa pracy oraz ochrony środowiska naturalnego. W wielu krajach istnieją przepisy dotyczące klasyfikacji substancji chemicznych oraz ich transportu i przechowywania, które muszą być przestrzegane przez przedsiębiorstwa zajmujące się produkcją czy obróbką chemikaliów. Przykładowo, wiele substancji organicznych stosowanych jako rozpuszczalniki podlega regulacjom dotyczącym ich emisji do atmosfery oraz odpadów chemicznych generowanych podczas procesu produkcji. Przemysł musi także dostosować swoje procedury operacyjne do wymogów dotyczących bezpieczeństwa pracy, co obejmuje m.in. szkolenie pracowników w zakresie obsługi urządzeń oraz postępowania w sytuacjach awaryjnych. Dodatkowo wiele krajów nakłada obowiązek regularnego przeprowadzania inspekcji technicznych sprzętu wykorzystywanego w procesach chemicznych, co ma na celu zapewnienie jego sprawności oraz zgodności z obowiązującymi normami bezpieczeństwa. Firmy muszą również prowadzić dokumentację dotyczącą używanych substancji chemicznych oraz ich wpływu na zdrowie ludzi i środowisko naturalne.